1 May 2025
The case for Hydrogen energy
The case for Hydrogen energy
Global energy consumption has quadrupled in the last 60 years. The world is undergoing another energy transition. The first one was at the beginning of last century, when the energy consumption from coal exceeded the one from biomass. The second one was in the ‘50s, when the energy consumption from oil and gas exceeded that of coal. The third one is happening now, and seeing renewables slowly ramping up and hopefully taking the place of oil and gas in the near future.
It is not certain when the transition will happen. But it is certain that it must happen, because fossil fuel is simply unsustainable as an energy source long-term: (i) it is the main driver of global warming, (ii) it is source of geopolitical tensions and inequalities, (iii) eventually, it will run out!
Hydrogen will be crucial in this third energy transition, and is expected to be involved in up to 15% of global energy consumption by 2050: (i) to achieve carbon neutrality, as the energy releasing process of hydrogen is carbon free; (ii) to empower large-scale applications of renewable energy, as energy storage carrier to match the intermittent power generation from renewables with load of demand.
Main use cases include: (i) transportation, as direct power source, e.g. fuell cell EV; (ii) energy, as a carrier for energy storage and power generation, e.g. in renewable power grids; (iii) industrial, as feedstock. Today, over 99% of total hydrogen demand is for industrial needs, although mostly grey hydrogen is used.
What do all hydrogen use cases have in common?
Hydrogen!
Hydrogen is approximately 1/14 as dense as air. It is highly buoyant, escapes easily, and disperse rapidly. In case of leakage in a confined space, hydrogen will accumulate at the top of that space. It is colorless and odorless, making it hard to sense when leakage occurs. It is highly flammable and explosive, with a wide explosive limit between 4% and 75% volume.
The fire caused by explosions is usually ferocious. It is necessary to adopt health and safety precautions. Hydrogen safety systems should include three aspects: (i) intrinsic safety; (ii) passive safety, of which hydrogen leakage detection is one of the pillars; (iii) active safety.
All hydrogen use cases need some form of hydrogen leak detection, and that is where Flusso comes into play!
Thermal conductivity gas sensing: the working principle
Our hydrogen sensing technology is based on heating and temperature sensing elements embedded within a dielectric membrane of a CMOS MEMS die. When the heater is OFF, nothing is happening.
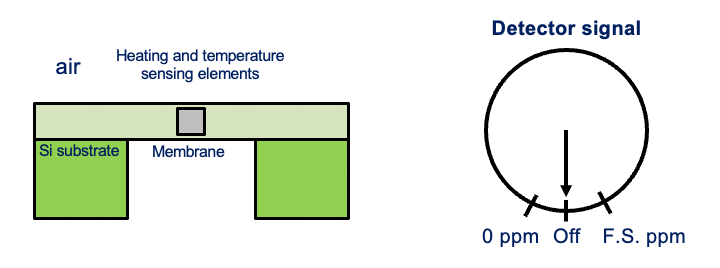
When current is injected in the heater, Joule heating takes place, and the heater reaches a target temperature.
This is driven by the equilibrium between the power dissipated through air, through the membrane, and through the cavity.
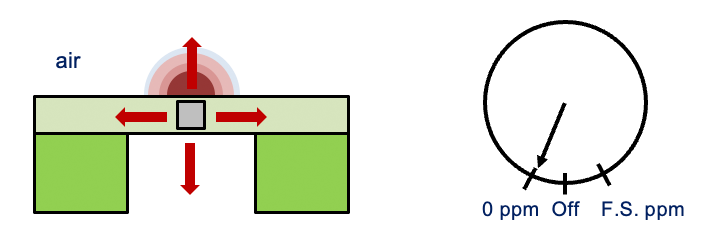
If H2 is present, its higher thermal conductivity vs. air causes higher power dissipation.
A calibration procedure allow us to correlate the power dissipation value with the hydrogen concentration, which is the information needed by the safety systems.
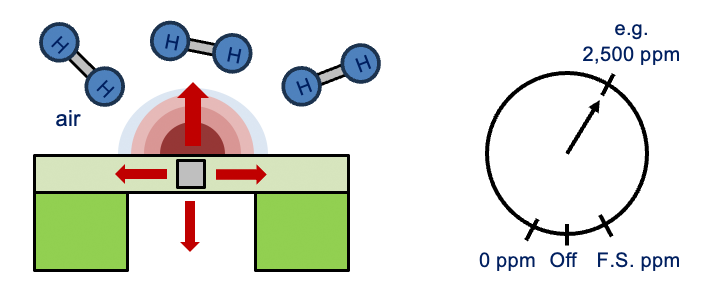
Catalytic vs. thermal conductivity gas sensing principles
Catalytic gas sensors are currently mainstream in the market, however thermal conductivity gas sensors show great promise!
Catalytic principle | Thermal conductivity principle |
---|---|
Chemical principle (catalytic combustion) | Purely physical principle, i.e. thermal |
Suffers from poisoning and catalyst consumption,
|
No poisoning/no catalyst consumption, and in turn
|
Cannot operate in low O2 environments | No need for O2 environment to function |
Limited range of detection (typically up to LEL) | 100% H2 detection range is possible |
Not easy to miniaturise and scale | Easily miniaturise-able and super-scalable |
High sensitivity in range of detection | Traditionally low sensitivitybut not with our technology! |
GSM5310 hydrogen leak detection sensor module & FLS310 thermal conductivity sensor
The GSM5310 Hydrogen Leak Detection Sensor Module is designed for leakage detection in hydrogen applications.
- Uses Flusso FLS310 thermal conductivity sensor
- Accuracy ± max (1000 ppm, 10% m.v.) across a temperature range of -40 – 85 ºC and humidity range of 0 – 40 g/m3
- Fast start up (<1 s) and response time (<4 s)
- High selectivity to hydrogen in humid air
- Very high immunity to poisoning
- CAN interface
- EvalKit available
The GSM5310 is an example of possible modules based around the FLS310. The FLS310 thermal conductivity sensor is suitable for high-volume consumer and industrial applications. Main features are:
- CMOS MEMS thermal conductivity technology
- Contains membrane crack detection circuit
- Ultra-small surface mount package (3×3 mm)
- Fully compatible with SMD assembly processes
Flusso is open to collaborate towards the development of customised sensor modules with FLS310 at their core. Let’s discuss your requirements!
"*" indicates required fields